Project 80
Updated: 10 November 2023
Location: Handsworth, Birmingham
Developer:
Midland Heart / Building Alliance / Birmingham City University
Number of units: 12 houses
Aim(s) of Project: Future Homes Standard
Construction method: Masonry - Insulated Cavity
Energy Compliance method: SAP 2013
Overheating compliance method: -
Construction start: -
Construction finish: September 2022

Overview of Project and Specification
12 conventional house-types produced using three different masonry construction solutions to give an 80-90% reduction from 2013 regulations, and so comply with the Future Homes Standard.
Cavities were 150mm (fully filled Xtratherm with a PIR core) with either a H+H aircrete block (with an airtight polymer spray) or Besblock Star Performer.
Design airtightness was either 1.5 m3/h/m2@50pa or 5 m3/h/m2@50pa.
Heating was ASHP or direct electric.
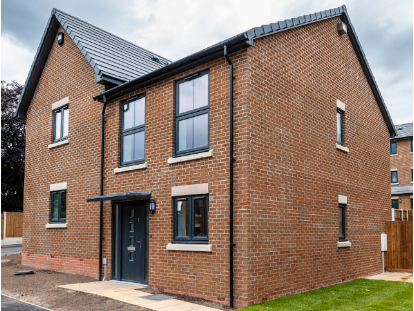
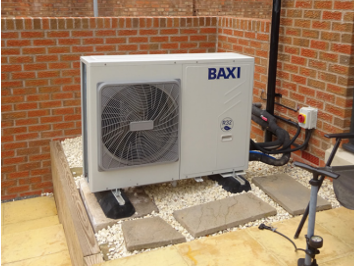
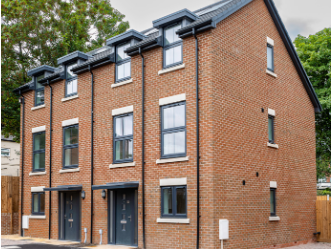
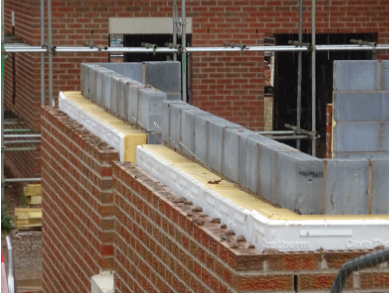
Key learnings
- These sort of wall compositions need to viewed as one system and require good buildable junction details. Brickwork contractors needed to be supported.
- Where it was used (to reduce air permeability) the polymer spray was accomplished successfully, but no one else can work in the house at the same time.
- The quality control of the fabric needs to be recognised within contracts that reflect the difficulties of wall composition.
- Glazing decisions are not purely based on performance, but also on weight, availability, security and maintenance,
- The M&E contractors were unfamiliar with some of the systems and needed valuable support from the heat pump manufacturers. The M&E contractor subcontracted the PV system which led to disconnects and the need for further co-ordination. Finding space in existing house layouts for hot water cylinders can be challenging.
- When installed the MVHR unit was placed in the loft and the duct work ran through the I-joists.
- Heat pump location, security and the installation of insulation/protection to pipework needs careful consideration. Common presentation of installation across manufacturers would be aid understanding and roll-out. Effective commissioning and on-going maintenance are essential. Contracts need to encourage meeting design performance.
- Controls need to be more user friendly. Handover must be carefully managed. Occupants need more information.
- Ventilation systems need to have a test certificate.
- Ventilation pathways, especially under doors need to be maintained (e.g. when fitting floors).
- Occupants need to understand their roll in achieving healthy air.
Performance evaluation
- Data on energy use has been collected (see interim project report). Monitoring is on-going and further reports will be published.
- Occupants are happy with their homes. Some residents reported that they no longer suffered from asthma since moving in.
- Occupants are struggling to understand how to use heat pumps efficiently despite, manuals webinars and visits. A bespoke user manual or app for houses built to the Future Homes Standard would help.
- Some occupants are opening windows all day. This appears to be because they lived in previous dwellings that were subject to mould.
- One resident commented on over-heating when the outside temperature exceeded 30 Celsius.